Cone Beam – Le GOLD standard de l’imagerie sectionnelle 3D en odonto-stomatologie
13 janvier 2025Optical impressions in odontology
13 janvier 2025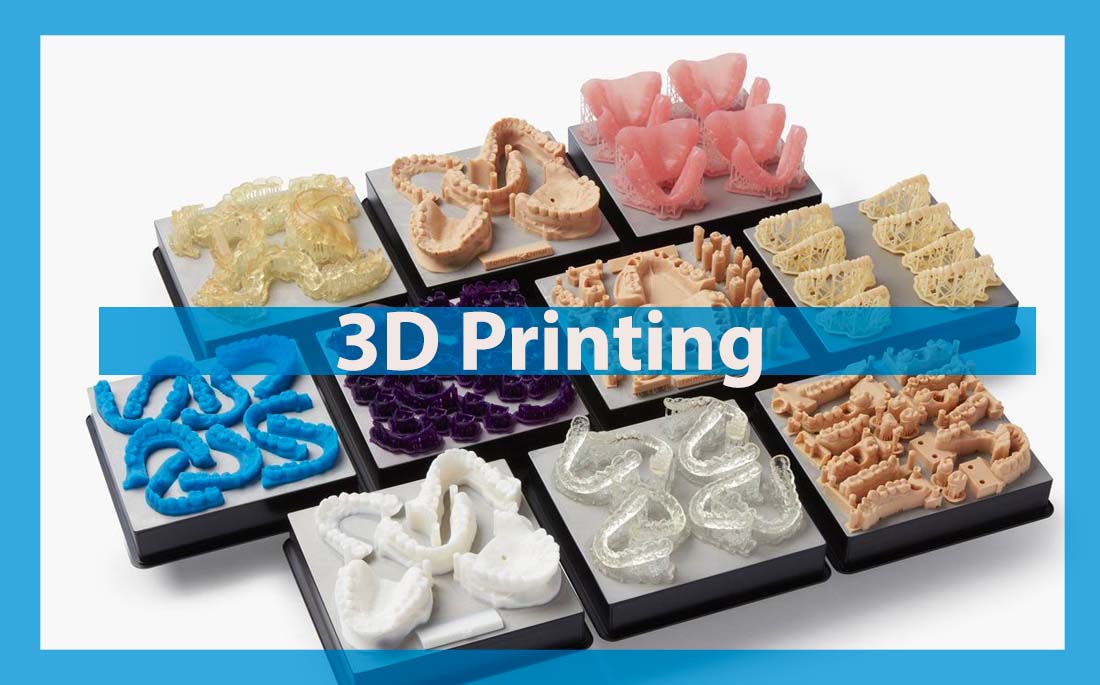
3D printing in dentistry
Introduction :
Developments in digital dentistry have seen the dental sector undergo tremendous change in recent years. In particular, additive manufacturing has enabled the dental industry to develop its use of digital technologies.
The dental sector is a market driver for 3D printing technology, as it responds to the issues of customisation.
A few key figures
In 2015, the 3D printing market for the dental industry was worth $780 million. According to SmarTech Publishing, a leading firm in market research creation for additive manufacturing, the medical sector (including dental) accounts for 11.3% of additive manufacturing technology users.
The firm also reports that the dental 3D printing market will grow to over $3.1 billion in 2020. This market is experiencing sharp annual growth estimated at over 35%, and is expected to tip $9.5 billion by 2027.
All of these promising figures demonstrate the various opportunities for additive manufacturing in this sector.
In this article on dental 3D printing, we’ll be detailing the techniques, materials and key uses of 3D printing technologies in dentistry, explaining the benefits and disadvantages of 3D printing for dentistry, and concluding with a look at the prospects for this innovative technique.
Dental 3D printing technologies:various procedures and materials
In industry, additive manufacturing is a process whereby a part is formed by adding another material, stacked in a succession of layers. 3D printing is the consumer name for the collection of additive processes.
In the dental industry, several technologies and materials are used in additive manufacturing.
The forming process can be physical (fusion followed by solidification, sintering) or chemical (photopolymerisation).
The technique selected depends on the application required.
Below are the main procedures used in dentistry.
FDM (Fused Deposition Modelling)
The technique involves depositing a thermoplastic filament heated to the plasticity temperature of polymer melt. In this case, the forming process is physical and uses thermoplastic materials (ABS or PLA).
FDM has the advantage of producing parts at low cost that require no post-processing. However, its drawbacks include a lack of speed, accuracy and biocompatibility. It is therefore only suitable for creating dental master models for thermoforming orthodontic alignment trays, retention trays or whitening trays.
Now, with the emergence of the latest thermoplastic material: PEEK (PolyEtherEtherKetone), this process can be used to produce biocompatible dental solutions, and, in particular, removable partial prostheses. This FDA-approved material boasts excellent chemical and mechanical resistance, while also being lightweight, for added patient comfort. Metal-free, this prosthesis has the advantage of being flavour-neutral.
Photopolymerisation
This is the main additive manufacturing process used in the dental sector. It’s a chemical procedure used in SLA (stereolithography) and DLP (Digital Light Processing) techniques.
SLA is the formation of a 3D model using successive layers, with a laser that sweeps each layer into a photosensitive liquid bath and polymerises it. The materials used are thermosetting plastics and elastomers.
This technology offers resolution and accuracy levels that are considerably higher than those of FDM, with biocompatible materials, all of which are liquid resins approved by the EC / FDA. The finish is much less complex, which reduces the overall manufacturing time.
This technology makes it possible to change materials for use with a different application. It can therefore be used to manufacture surgical guides, temporary prostheses, and burn-out elements, such as stellite components.
Metal additive manufacturing
Depicted mainly by SLM (Selective Laser Melting or Fusion Laser) and SLS (Selective Laser Sintering), additive manufacturing is used to make implants, stellites and nickel-chrome copings.
This technology needs sustained production in order to cushion the sizeable investment required.
Metal machines will also require more significant post-processing work, thereby reducing productivity; in terms of unit cost, however, this technology remains considerably more attractive.
Materials processes
Selective Laser Melting (SLM) or Laser Metal Fusion +++
Plastics
Ceramics
Selective Laser Sintering (SLS) or Metal Laser Sintering +++
Thermoplastics (polycarbonate, polyamides, polyvinyl chloride)
Ceramics
FDM (Fused Deposition Modelling) Thermoplastics (ABS or PLA)
Stereolithography (SLA)
Thermoset elastomers and plastics
Applications for 3D printing in dentistry
3D printing has chiefly been adopted by dentistry professionals wanting to produce surgical guides, customised dental trays, burn-out resin parts, impressions for moulds and temporary dental crowns.
3D printing applications in dentistry fall into three categories:
Manufacturing directly from bespoke dental devices:
These are mainly implant surgical guides that can guide the surgeon during the drilling process and thereby respect the digital pre-implant plan, including implant location, angulation and depth.
Using class III biocompatible resins, it is also possible to print 3D trays that are comfortable and perfectly adapted to the patient’s mouth, including whitening, bruxism and fluoride gel trays.
3D printing can also be used to make devices used in DFO, such as alignment and transfer trays, osteotomy guides and repositioning guides, as well as all kinds of orthoses and interception devices.
Devices for maxillo-facial surgery (genioplasty, rhinoplasty, epistheses) can also be printed in 3D.
3D impression printing for dental moulds using the lost-wax technique
A 3D version of dental prostheses (crowns, bridges, etc.) printed using burn-out resin and used to make a customised mould harnessing the lost-wax technique. The final prosthesis is obtained by pouring the desired material (ceramic, metal, etc.) into this mould.
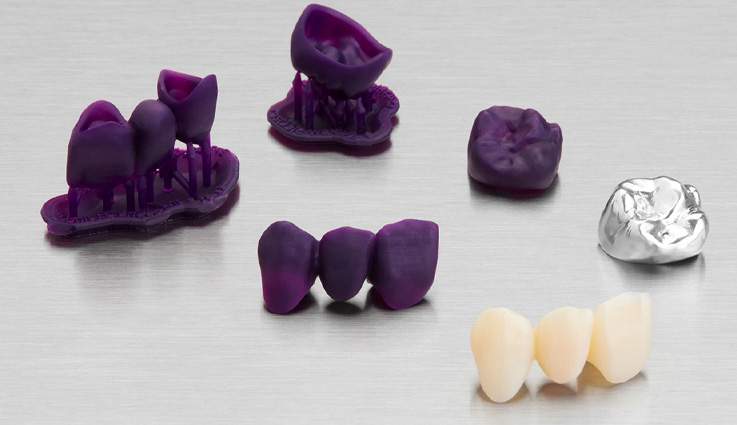
Figure 1 A 3D printed dental crown (lost-wax technique)
Direct manufacturing of dental restorations and prostheses
Thanks to 3D printing, it is now possible to make temporary veneers, crowns and bridges with biocompatible resins. These restorations are perfectly adjusted to the patient’s mouth, thanks to the high precision of 3D scanning and SLA and DLP resin 3D printers.
However, it should be noted that it is not yet possible to directly print permanent crowns or dental prostheses in 3D, either in resin or ceramic.
Metal additive manufacturing makes it possible to produce crowns, bridges and dental implants, as well as the metal part of dental stellites and the base of removable complete prostheses.
A technique for every application
Technical application
Surgical guides SLA
Temporary SLA prostheses
DFO Orthoses, interception devices, dental trays, SLA models
Maxillo-facial surgery (genioplasty, rhinoplasty, epitheses) and DFO: Osteotomy guide and repositioning guide, e.g. Lefort orthognathic surgery, mandibular reconstruction, etc. SLA
Bases of removable complete prostheses
FDM
Metal frame for removable partial prostheses
Metal additive manufacturing
The benefits of 3D printing for the dental industry
In today’s prosthetics laboratories, it is not uncommon to see various solutions coexisting, solutions that are both subtractive and additive as part of a digital work flow strategy.
Using 3D printing to complement traditional machining methods offers many advantages.
A dematerialised and simplified manufacturing process
Traditionally, prostheses were the result of a collaboration between dentist and prosthetist. The advent of digital technologies has shaken up this traditional organisation, by completely dematerialising working processes.
Both of these dentistry players are now part of a drive to modernise their latest tools, while retaining their expertise, which remains paramount.
By using additive manufacturing, it is possible to simplify the production chain through digital flows, optimise conditions and reduce prosthetic and dental mould manufacturing cycles, and, consequently, the delicate manual work stages.
Speed
From digital dental impressions to manufacturing using 3D printing, the fully digital process requires only a few hours’ work instead of the several days traditionally required. In some cases, these shorter manufacturing times mean that the patient is only called in once.
By reducing the number of man hours, using additive manufacturing can be used to reallocate these hours to work with greater value added, considerably raising productivity.
Profitability
3D printing has a high ROI, which explains its adoption by a large number of dental surgeons and prosthetists worldwide.
Today, over 50% of French prosthetics laboratories are fitted with 3D scanners and processors, and 20% with 3D printers, enabling them to boost their turnover by 70%.
Additive manufacturing is extremely profitable, as several prostheses can be printed simultaneously, meaning economies of scale in terms of both time and cost.
High precision parts
Additive manufacturing techniques, involving adding materials, further increase the degree of accuracy.
The quality of parts made compares very favourably to those produced by traditional methods used in the dental industry.
The main advantage of 3D printing lies in its ability to produce customised, bespoke parts.
Advantages for the patient
Combining digital techniques makes it possible to produce customised dental devices and prostheses in record time, which in turn has benefits for patient comfort as well as treatment effectiveness.
Ecological aspect
Additive technologies are recognised for their low energy consumption. They are environmentally friendly, and have a smaller impact on the ecosystem.
The materials used are generally biodegradable and recyclable, therefore more sustainable.
Disadvantages
Clearly, 3D technologies offer considerable advantages; however, some practitioners may be reluctant to adopt them, after years working with traditional methods.
Switching to digital means having a certain degree of confidence in these processes. Dentist and prosthetist converts are required to acquire the necessary equipment, the use of which involves a new organisation and working system, as well as training, in order to master the software and devices.
Looking ahead
SmarTech Publishing explains that resin 3D printing solutions, which cost less than $5,000, will play a key role in the growth of 3D printing in the dental industry.
The firm estimates that over the last two years, Formlabs increased its market share by over 20 times with its Form 2 3D printer and certified dental resins.
SmarTech says that over the next ten years, additive manufacturing will become the main production method for all dental restorations, eventually covering the entire range of dental prostheses; metal additive manufacturing in particular should play an important role in this sector, especially for direct metal implant production.
The report estimates that turnover for externalised metal implant 3D printing will exceed a billion dollars by 2024.
Conclusion
With its myriad techniques and materials, 3D printing has established itself in the dental sector by virtue of its flexibility in production, its efficiency, its speed and its accuracy.
Additive techniques can be used to optimise manufacturing processes for prosthetics and various dental devices that have long been dominated by machining technology, without compromising the end quality of these products.
Their main advantage lies in the manufacturing of customised devices, which is a major problem area in medicine, and particularly in dentistry.
All the data points to promising dental market growth that can derive maximum benefit from digital technology.